1. Structure and distribution of joints
(1) Distribution of human joints
Since the former Tesla's robot realized 28 degrees of freedom, which is equivalent to about 1/10 of the human body's function.
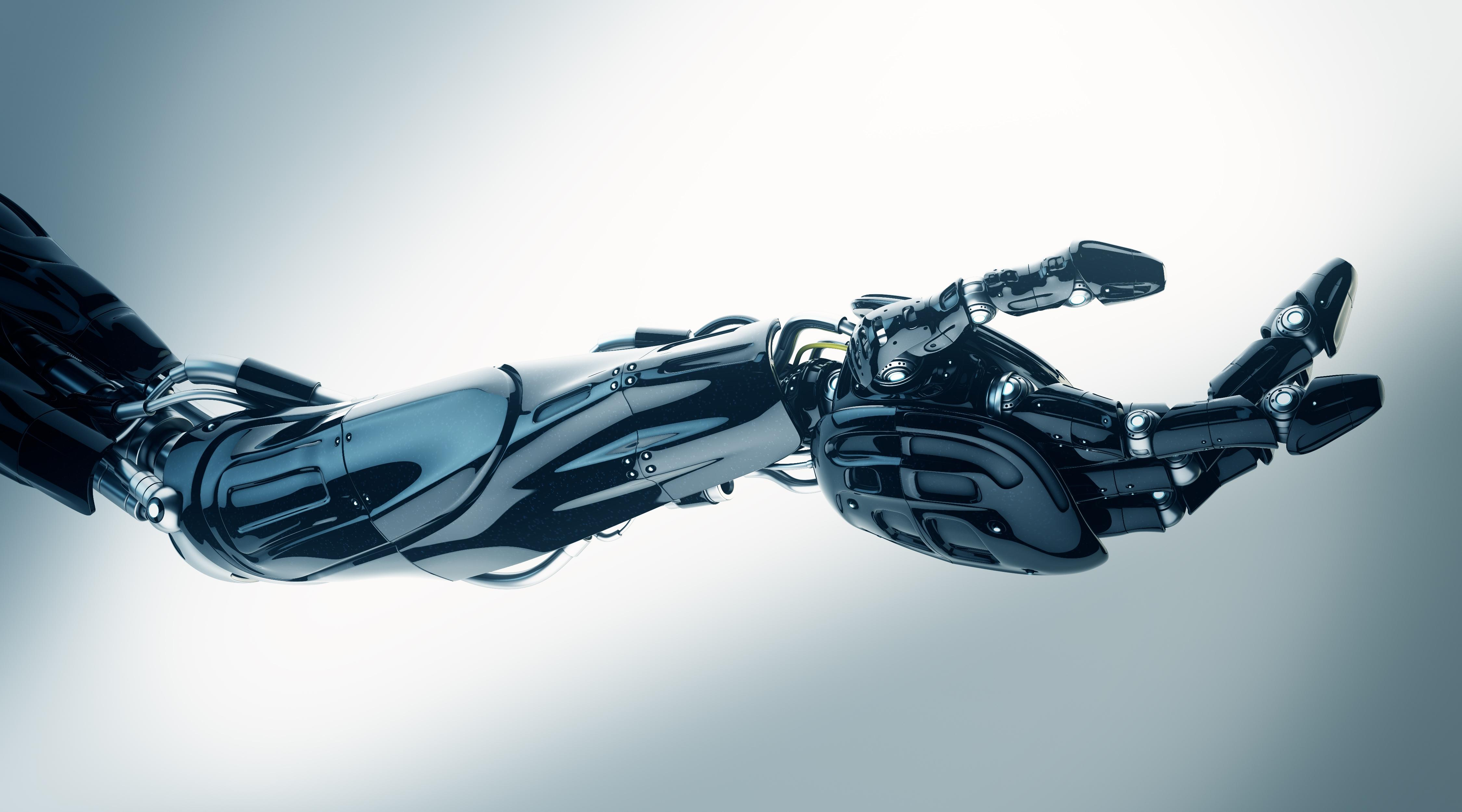
These 28 degrees of freedom are mainly distributed in the upper and lower body. The upper body includes the shoulders (6 degrees of freedom), elbows (4 degrees of freedom), wrists (2 degrees of freedom) and waist (2 degrees of freedom).
The lower body includes the medullary joints (2 degrees of freedom), thighs (2 degrees of freedom), knees (2 in degrees of freedom), calves (2 degrees of freedom) and ankles (2 degrees of freedom).
(2) Type and strength of joints
These 28 degrees of freedom can be categorized into rotational and linear joints. There are 14 rotary joints, which are divided into three subcategories, differentiated according to the rotational strength. The smallest rotary joint strength is 20 Nm used in the arm: 110 born 9 in used in the waist, medulla and shoulder, etc.: 180 in used in the waist and hip. There are also 14 linear joints, differentiated according to the strength. The smallest linear joints have a strength of 500 oxen and are used in the wrist; 3900 oxen are used in the leg; and 8000 oxen are used in the thigh and knee.
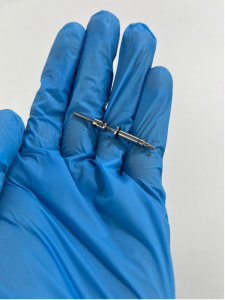
(3) Structure of the joint
The structure of the joints includes motors, reducers, sensors and bearings.
Rotary joints use motors and harmonic reducers,
and more optimized solutions may be available in the future.
Linear joints use motors and ball or ball screws as reducers, along with sensors.
2. Motors in humanoid robot joints
The motors used in the joints are mainly servo motors rather than frameless motors. Frameless motors have the advantage of reducing weight and removing extra parts to achieve greater torque. Encoder is the key to closed-loop control of the motor, and there is still a gap between domestic and foreign in the accuracy of the encoder. Sensors, force sensors need to accurately sense the force at the end, while position sensors need to accurately sense the robot's position in three-dimensional space.
3. Application of reducer in humanoid robot joints
Since the previous mainly used harmonic reducer, consisting of the transmission between the soft wheel and the steel wheel. Harmonic reducer is effective but expensive. In the future, there may be a trend for planetary gearboxes to replace harmonic gearboxes because planetary gearboxes are relatively cheap, but the reduction is relatively small. According to the actual demand, there may be a part of the planetary gearbox is adopted.
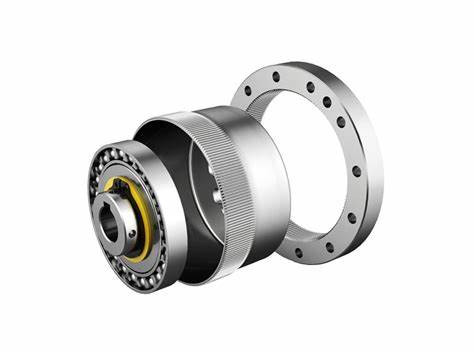
The competition for humanoid robot joints mainly involves reducers, motors and ball screws. In terms of bearings, the differences between domestic and foreign enterprises are mainly in precision and life span. In terms of speed reducer, planetary speed reducer is cheaper but less deceleration, while ball screw and roller screw are more suitable for finger joints. In terms of motors, domestic enterprises have a certain degree of competitiveness in the field of micro motor.
Post time: May-19-2025